Golf balls are a crucial piece of equipment for any golfer, but have you ever wondered how they are made? The process of manufacturing a golf ball is complex and involves a combination of materials, design elements, and production techniques. Understanding how golf balls are made can help golfers appreciate the craftsmanship that goes into producing these small but mighty spheres.
The history of golf ball manufacturing dates back centuries, with early balls being made from materials like wood, feathers, and gutta-percha. Over time, advances in technology and materials have led to the production of synthetic golf balls made from materials like urethane and surlyn. Today, golf balls are made using a multi-step process that involves the formation of the core, the application of the mantle layers, and the application of the cover.
In this article, we will take a detailed look at the manufacturing process of golf balls. We will explore the composition and design of golf balls, as well as the manufacturing techniques used to produce them. We will also discuss the various types of golf balls on the market and the environmental impact of golf ball production. By understanding how golf balls are made, golfers can make informed decisions about which balls to use on the course and gain a greater appreciation for the craftsmanship behind this essential piece of golf equipment.
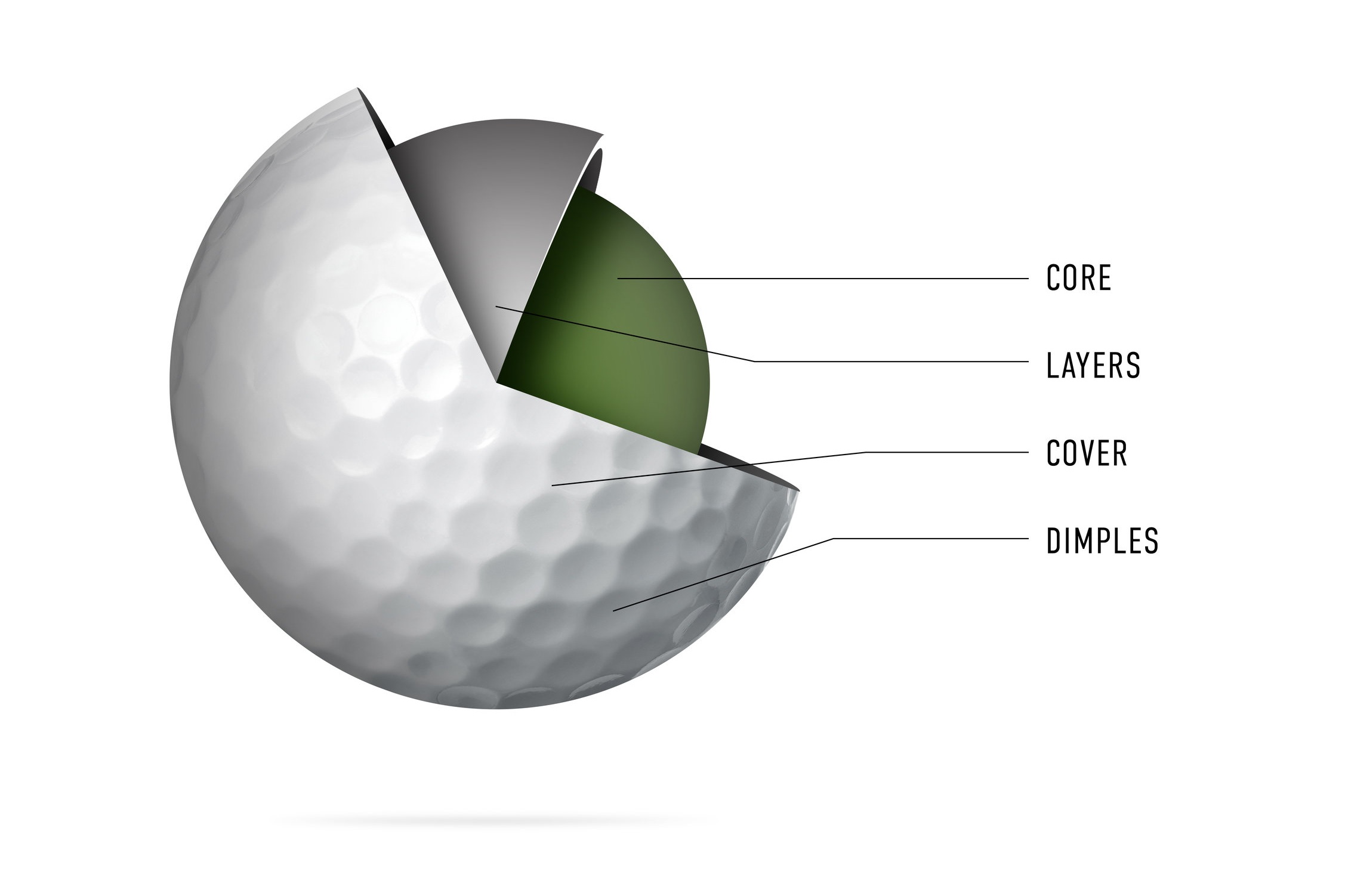
History of Golf Ball Manufacturing
The history of golf ball manufacturing dates back to the 14th century, when players used wooden balls. Over time, balls were made from a variety of materials, including feathers, gutta-percha, and rubber. Today, most golf balls are made from synthetic materials, such as urethane and surlyn, and involve a multi-step manufacturing process.
The Composition of Golf Balls
The core, mantle layers, and cover of a golf ball all play an important role in determining its performance on the course. The core of a golf ball is typically made from a rubber-like material and is responsible for the ball’s initial velocity and compression. The mantle layers, which are made from materials like ionomer and high-energy rubber, help to increase the ball’s velocity and reduce spin. The cover of a golf ball is made from a soft, thin material like urethane and helps to control spin and provide feel.
Golf Ball Manufacturing Process
The manufacturing process of a golf ball involves several steps, from forming the core to applying the cover. The core is typically formed by combining a mixture of rubber-like materials, additives, and fillers, which are then molded into a sphere. The mantle layers are then applied to the core using a molding process, and the cover is applied using a similar process. The ball is then painted and finished, and undergoes quality control and testing before being packaged for shipment.
Types of Golf Balls
There are several different types of golf balls on the market, each designed for specific swing speeds and skill levels. For example, low-compression balls are designed for golfers with slower swing speeds, while high-compression balls are designed for more advanced players with faster swing speeds. There are also balls designed for maximum distance, control, and feel.
Sustainable Golf Ball Manufacturing
As golf continues to grow in popularity, there has been increased attention on the environmental impact of golf ball production. While synthetic materials are often used in golf ball manufacturing, some companies are exploring more sustainable options, such as biodegradable materials and recycling programs.
Conclusion
The manufacturing process of a golf ball is a complex and multi-step process that involves a combination of materials, design elements, and manufacturing techniques. Understanding how golf balls are made can help golfers appreciate the level of craftsmanship that goes into producing these small but mighty spheres. By considering the composition, design, and production of golf balls, golfers can make informed decisions about which balls to use on the course. As sustainability becomes an increasingly important consideration in golf ball production, it is likely that we will see continued innovation in this area in the years to come.