Golf is a game of precision and skill, and at the center of it all lies the humble golf ball. It may seem like a simple sphere, but the intricate process of crafting a golf ball involves a blend of science, engineering, and meticulous craftsmanship. Have you ever wondered how these small yet essential pieces of golf equipment are made?
In this article, we will take you on a journey through the fascinating world of golf ball manufacturing. From the core to the cover, and from the dimples to the finishing touches, we will explore the step-by-step process that transforms raw materials into high-performance golf balls.
The core, the heart of the golf ball, determines its resilience and energy transfer upon impact. We will delve into the various core materials used and their impact on ball compression and performance. Moving on, we will examine the cover materials and designs, exploring their influence on spin control, durability, and overall feel.
But the manufacturing process doesn’t end there. We will uncover the meticulous steps involved in molding the core, applying the cover, and adding the finishing touches that make each golf ball unique. Quality control and testing protocols play a crucial role in ensuring that every ball meets the required standards.
So, join us as we unravel the secrets behind the creation of these small spheres that bring joy, frustration, and countless memorable moments on the golf course. Let’s explore how golf balls are made and gain a deeper appreciation for the craftsmanship that goes into crafting these essential tools of the game.
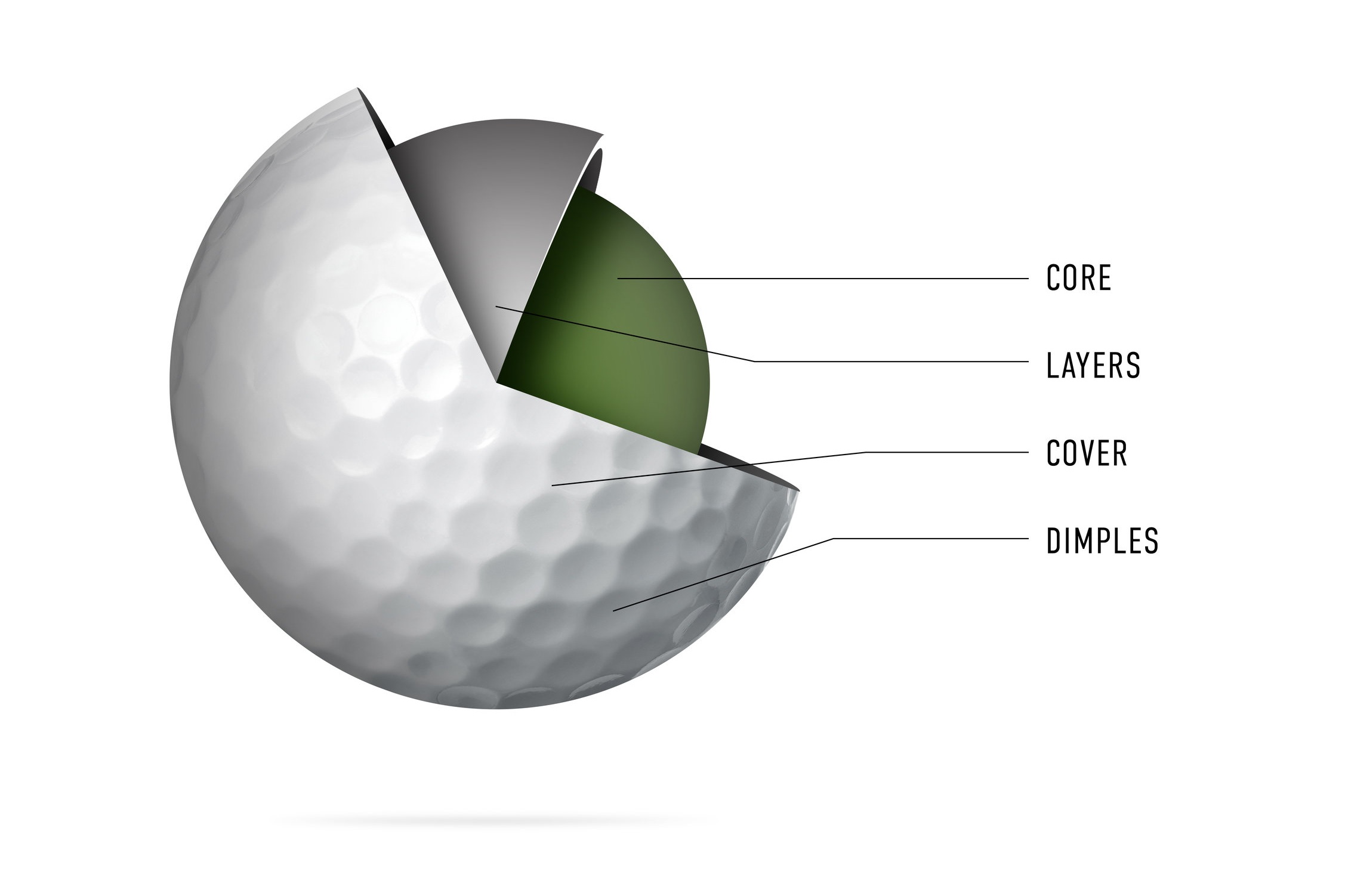
The Core of a Golf Ball
At the heart of every golf ball lies its core. The core is a critical element that significantly impacts the performance characteristics of the ball. Let’s delve into the construction and composition of golf ball cores.
What is the core of a golf ball?
The core is the innermost layer of the golf ball, responsible for providing its resilience and energy transfer. It is typically made of rubber or synthetic materials. The core’s size, compression, and construction can vary, leading to different ball flight characteristics and performance.
Construction of the core
Golf ball manufacturers employ various core designs to achieve desired performance attributes. Let’s explore some core materials and their significance in the construction process.
Types of core materials used
- Solid rubber cores: Traditional golf balls feature solid rubber cores that provide a consistent feel and distance. These cores are molded from a solid piece of rubber, offering a predictable response upon impact.
- Dual-core construction: Modern golf balls often employ a dual-core construction, where an inner core is surrounded by an outer core. This design enhances energy transfer and allows for greater control and distance.
- Multilayered cores: High-performance golf balls may feature multilayered cores consisting of multiple layers with varying properties. These complex core constructions enable customization of performance, offering a balance of distance, spin control, and feel.
Understanding the role of core materials and their impact on ball compression and energy transfer is crucial in comprehending the performance characteristics of golf balls.
Cover Materials and Designs
The cover of a golf ball not only provides protection but also contributes to its spin control, durability, and overall feel. Let’s explore the different cover materials and designs employed in golf ball manufacturing.
Different types of golf ball covers
Golf ball covers can be made from various materials, each offering unique characteristics. Here are some common cover materials used in the industry:
- Surlyn covers: Surlyn is a durable and cost-effective material often used in lower-priced golf balls. It provides excellent cut and abrasion resistance, ensuring the ball retains its shape and durability over time.
- Urethane covers: Urethane covers are favored by many professional golfers and experienced players due to their exceptional feel and control. These covers offer enhanced spin performance, allowing players to manipulate the ball’s trajectory and have precise control around the greens.
- Balata covers (historical relevance): Balata covers were popular in the past but have become less common today. They offer a soft feel and high spin rates, providing excellent control for skilled players. However, balata covers are more susceptible to cuts and wear.
Factors influencing cover material selection
Golf ball manufacturers consider several factors when selecting the appropriate cover material for a particular ball model. Let’s explore these factors:
- Durability and resistance to scuffs and cuts: The cover material should be durable enough to withstand the rigors of play and resist scuffs and cuts caused by club impacts and contact with various surfaces.
- Spin control and feel on impact: The cover material affects the ball’s ability to generate spin, providing players with control over the ball’s flight and stopping power on the greens. The material’s softness or firmness influences the feel experienced by the golfer upon impact.
- Cost considerations: The cost of materials plays a role in determining the final selection of cover materials. Manufacturers aim to strike a balance between performance characteristics and affordability to cater to different market segments.
Dimple designs and their impact on ball flight
While the core and cover materials are crucial, the dimples on a golf ball’s surface also play a vital role in its aerodynamic performance. Let’s explore the significance of dimples and the various designs used.
- Aerodynamics of dimples: Dimples alter the airflow around the ball, reducing drag and optimizing lift. They create a thin turbulent boundary layer, allowing the ball to achieve greater distances and maintain stability during flight.
- Different dimple patterns and their effects on lift and drag: Golf ball manufacturers employ a variety of dimple patterns to fine-tune the ball’s aerodynamic characteristics. These patterns affect the lift and drag forces acting on the ball, influencing its trajectory and overall performance.
Now that we’ve explored the core, cover materials, and dimple designs, let’s dive into the intricate manufacturing process of golf balls.
Manufacturing Process
The manufacturing of golf balls involves a series of precise steps to ensure consistent quality and performance. Let’s take a closer look at the key stages in the manufacturing process.
Preparing the core
The core manufacturing process begins with the molding and curing of the core material. The following steps are involved:
- Core molding and curing: The chosen core material is shaped into a spherical form using specialized molds. The molded cores are then subjected to heat and pressure to cure and solidify them, imparting the desired properties.
- Quality control and inspection: To maintain consistent quality, each core undergoes rigorous inspection to check for defects, size accuracy, and compression levels. Any cores that fail to meet the predetermined specifications are discarded.
Adding the cover
Once the cores are ready, the next step is to add the cover material. This process involves compression and application techniques:
- Cover compression and application: The molded cores are placed in a machine that applies pressure and heat to compress the cover material onto the core. This process ensures a secure bond between the core and the cover, creating a seamless outer surface.
- Heat and pressure treatment: After the cover is applied, the golf balls undergo additional heat and pressure treatment to enhance the bond between the core and the cover. This step ensures durability and consistency in the finished product.
Finishing touches
With the core and cover in place, the golf balls go through the final stages of production:
- Printing and branding: Golf ball manufacturers imprint logos, brand names, and alignment aids onto the surface of the balls. This step involves precise printing techniques to ensure clear and durable markings.
- Application of final coatings and finishes: To protect the ball and enhance its performance, a final coating or finish is applied. This coating may provide additional durability, resistance to scuffs, or specific characteristics such as high visibility.
The manufacturing process is nearing completion, but before the golf balls are ready for market, stringent quality control and testing protocols are implemented.
Quality Control and Testing
Quality control is of paramount importance in golf ball manufacturing to ensure consistency and adherence to performance standards. Let’s explore the crucial aspects of quality control and testing.
Importance of quality control in golf ball manufacturing
Quality control is essential to deliver golf balls that meet the expected performance standards, as well as to maintain brand reputation and customer satisfaction. Stringent quality control measures are implemented throughout the manufacturing process to identify and rectify any issues or defects.
Testing the performance of golf balls
Various tests are conducted to evaluate the performance characteristics of golf balls. Here are some commonly employed testing methods:
- Compression testing: Golf balls are subjected to compression tests to determine their hardness or softness. Compression values indicate the ball’s responsiveness and feel upon impact, providing valuable information for players to select the right ball for their game.
- Ball flight and trajectory analysis: Golf balls are tested for their flight characteristics, including launch angle, spin rates, and overall trajectory. This analysis helps golfers understand how the ball performs in terms of distance, accuracy, and ball flight control.
- Spin rate and distance testing: Golf balls undergo tests to measure their spin rates and distance performance. These tests evaluate the ball’s ability to generate spin for enhanced control around the greens and assess its overall distance potential.
By conducting rigorous quality control and testing, manufacturers ensure that each golf ball meets the required specifications and performs consistently on the course.
Regulations and Standards
The world of golf follows regulations and standards to ensure fair play and maintain a level playing field. Let’s delve into the regulations governing golf balls and the organizations responsible for setting these standards.
Golf ball regulations and governing bodies
Golf ball regulations are established and enforced by organizations such as the United States Golf Association (USGA) and The R&A. These governing bodies aim to maintain the integrity of the game and ensure that golf balls meet specific criteria for size, weight, and performance.
Specifications for golf ball size, weight, and performance
The USGA and The R&A have established specific guidelines and specifications for golf balls. These include parameters such as maximum size, weight, initial velocity, and overall performance limits. Manufacturers must ensure their golf balls adhere to these standards to be eligible for use in regulated tournaments and competitions.
Conformance testing and certification
To certify compliance with regulations, golf ball manufacturers conduct conformance testing. This involves rigorous examination and evaluation of various aspects, including size, weight, initial velocity, and overall performance characteristics. Balls that pass these tests are then certified as conforming to the regulations set forth by the governing bodies.
Non-compliance with regulations can have consequences, such as disqualification from tournaments or loss of trust in the market. Therefore, adherence to the established standards is crucial for manufacturers in the golf ball industry.
Innovations and Future Trends
The world of golf is constantly evolving, and golf ball technology continues to advance. Let’s explore some recent innovations and future trends shaping the manufacturing of golf balls.
Recent advancements in golf ball technology
Manufacturers are continually pushing the boundaries of golf ball performance. Some recent advancements include:
- High-performance multi-layered constructions: Golf balls with advanced multilayered constructions, including dual cores and mantle layers, offer optimized performance in terms of distance, spin control, and feel. These constructions allow for customized performance suited to different playing styles.
- Enhanced aerodynamics and dimple designs: Ongoing research and development focus on refining dimple patterns and aerodynamics to reduce drag, increase lift, and optimize ball flight. Improved aerodynamics result in longer distances and enhanced accuracy.
Emerging trends in golf ball manufacturing
The future of golf ball manufacturing holds exciting possibilities. Here are some emerging trends to watch for:
- Sustainable and eco-friendly materials: As environmental concerns grow, there is an increasing emphasis on developing golf balls using sustainable materials and manufacturing processes. Biodegradable covers and eco-friendly core materials are being explored to reduce the environmental impact of golf ball production.
- Customization options for golfers: Golf ball manufacturers are exploring ways to offer customization options to golfers. This includes personalized markings, color choices, and even individualized performance attributes tailored to a golfer’s swing characteristics and preferences.
As technology advances and consumer demands evolve, golf ball manufacturers are committed to pushing the boundaries of innovation, delivering improved performance, and enhancing the overall golfing experience.
Conclusion
The manufacturing process of golf balls involves intricate steps, combining core construction, cover materials, and dimple designs to create high-performance equipment for golfers. The attention to detail and quality control ensures that each golf ball meets the required specifications for size, weight, and performance. Regulations set by organizations like the USGA and The R&A provide guidelines to maintain fairness and integrity in the game of golf.
Recent advancements in golf ball technology, such as high-performance multi-layered constructions and enhanced aerodynamics, have revolutionized the game, offering players greater distance, control, and feel. Additionally, emerging trends focus on sustainability, with the development of eco-friendly materials and customization options that cater to individual golfer preferences.
In conclusion, the manufacturing of golf balls is a complex process that involves the careful selection of core materials, cover materials, and dimple designs. Quality control and adherence to regulations ensure consistent performance and reliability. With ongoing innovations and future trends, golf ball technology continues to evolve, pushing the boundaries of performance and enhancing the overall golfing experience. So, the next time you tee up a golf ball, take a moment to appreciate the craftsmanship and engineering that goes into creating this small but essential piece of equipment for the game you love.